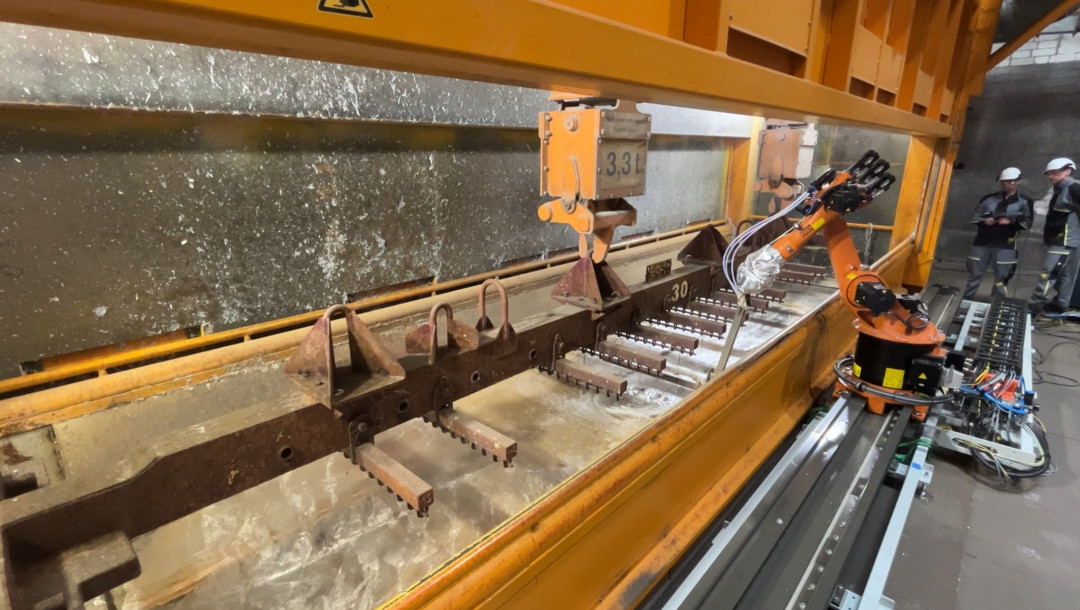
In der Feuerverzinkungsbranche sind Beschäftigte während des Verzinkungsprozesses, insbesondere beim manuellen Abscheiden von Zinkasche, hohen Risiken für ihre Sicherheit und ihre Gesundheit ausgesetzt.
Um diese Risiken zu minimieren, wurde in einem gemeinsamen Forschungsprojekt der Berufsgenossenschaft Holz und Metall (BGHM), des Fraunhofer IFF und dem IEHK der RWTH Aachen der Einsatz von Automatisierungstechnik im Verzinkungsprozess untersucht und an einem realen Verzinkungsofen im Industriereinsatz erprobt.
Prozess in 450 °C heißem Zink
Beim Feuerverzinken wird das vorbehandelte und an einer Traverse befestigte Verzinkungsgut in einen Verzinkungskessel mit flüssigem, etwa 450° C heißem Zink getaucht. Während der rund 10 Minuten, die der Prozess dauert, reagieren das Zink, die Luft und das Flussmittel miteinander, wodurch verschiedene Reaktionsprodukte entstehen.
Diese lagern sich auf der Zinkbadoberfläche ab und beeinträchtigen die Qualität der Zinkschicht, wenn das Verzinkungsgut aus der Schmelze herausgehoben wird. Besonders im Fokus steht die Zinkasche, die durch die Verdampfung des Flussmittels entsteht und sich auf der Zinkschmelze ablagert.
Diese Asche muss als Teil des Gesamtprozesses manuell entfernt werden. Beschäftigte am Verzinkungsofen schieben mit Hilfe eines mechanischen Rechens die Zinkasche von der Oberfläche zur Stirnseite des Verzinkungskessels. In diesem
Prozess sind die Beschäftigten einigen Risiken ausgesetzt. So besteht zum Beispiel die Gefahr des Absturzes in die Zinkschmelze. Zudem bestehen auch Gefährdungen durch das Einatmen von Dämpfen.
Gesundheitsrisiken minimieren
Dr. Andreas Voßberg von der der Berufsgenossenschaft Holz und Metall (BGHM), betont:
„Das Einatmen von Gefahrstoffen aus dem aufsteigenden Zinkrauch ist eine ernsthafte Gefahr für die Gesundheit der Mitarbeiter.“
Eine Automatisierung der Zinkascheabscheidung könnte diese Risiken signifikant reduzieren und gleichzeitig den Personalbedarf an den Industrieverzinkungskesseln verringern.
Das gemeinsame Forschungsprojekt der Berufsgenossenschaft Holz und Metall (BGHM), des Fraunhofer IFF und dem IEHK der RWTH Aachen hat sich dieser Fragestellung angenommen. Es baut auf einer erfolgreich abgeschlossenen Machbarkeitsstudie auf. Dabei sollen die im Labormaßstab gewonnenen Ergebnisse auf den industriellen Einsatz übertragen werden.
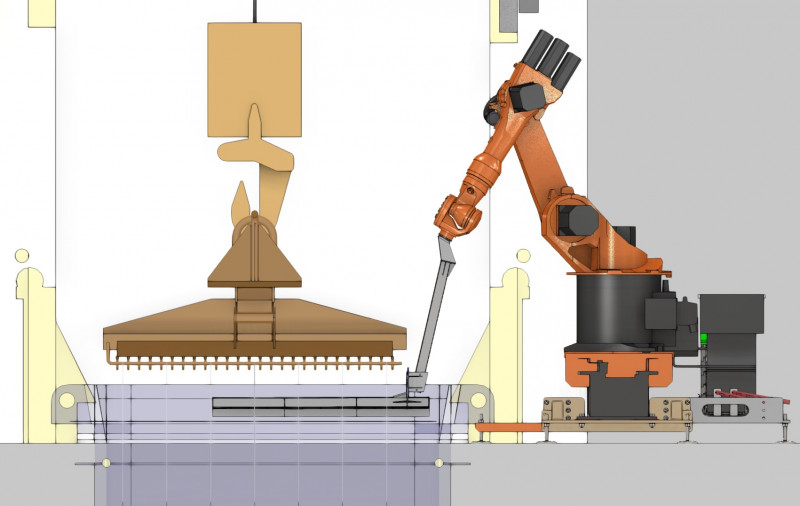
Der automatisierte Prozess ist an den typischen manuellen Arbeitsabläufen der Feuerverzinkungsbranche ausgerichtet, die von den Beschäftigten beim Zinkascheabscheiden durchzuführen sind. Das Abscheidewerkzeug wird dazu an einen 6-achsigen Industrieroboter montiert, der auf einer Linearachse entlang des Verzinkungsofens bewegt werden kann.
Dieses Werkzeug wird dann innerhalb des Verzinkungsofens in den Raum zwischen den Warenträgern platziert und bewegt. Dabei wird die Zinkasche auf der Oberfläche der Zinkschmelze weggeschoben. Diesen Prozess vollständig zu automatisieren und in realer Umgebung einzusetzen, ist das Ziel des Projektes.
Torsten Felsch vom Fraunhofer IFF, erklärt:
„Die Nutzung eines Roboters ermöglicht eine präzisere und sicherere Handhabung, insbesondere in Bereichen, in denen menschliche Eingriffe gefährlich sein könnten.“
Automatisierung soll Sicherheit verbessern
In einem ersten Schritt wurden geeignete Abscheidewerkezeuge für den Industriekessel entworfen und konstruiert. Zum Einsatz sollten ein gasbasiertes Abscheidesystem (Düse) und ein mechanisches Abscheidewerkzeug (Rechen) kommen.
Die folgenden Kriterien wurden dazu als Richtlinien formuliert:
- Gewicht: Das maximale Gewicht des Abscheidewerkzeugs ist abhängig vom eingesetzten Roboter, d.h. von zulässigen Lastmomenten in den Robotergelenken (insbesondere am Flansch zwischen den Abscheidewerkzeugen und der Roboterhand)
- Abmessungen: Werkzeuge müssen an den Verzinkungskessel angepasst werden.
- Wärmebeständigkeit: Materialien müssen Temperaturen von bis zu 450 °C standhalten.
- Stabilität und Steifigkeit: Hohe Anforderungen aufgrund der Dichte des Zinks.
- Modularität: Werkzeuge sollten modular aufgebaut sein, um Reparaturen zu erleichtern.
Mit den konstruierten Abscheidewerkzeugen wurden sowohl praktische Vorversuche als auch theoretische Berechnungen durchgeführt. Dabei kam zunächst ein Holzmodell des Verzinkungsofens im Maßstab 1:1 im Technikum des Fraunhofer IFF zum Einsatz, in dem mit Wasser und Kunststoffpartikeln die relevanten Prozessparameter für den späteren Einsatz am Industrie-Verzinkungsofen ermittelt wurden. Durch diese Vorversuche wurde wertvolle
Erkenntnisse gewonnen, die dabei halfen, die Effizienz der automatisierten Abscheidung zu maximieren.
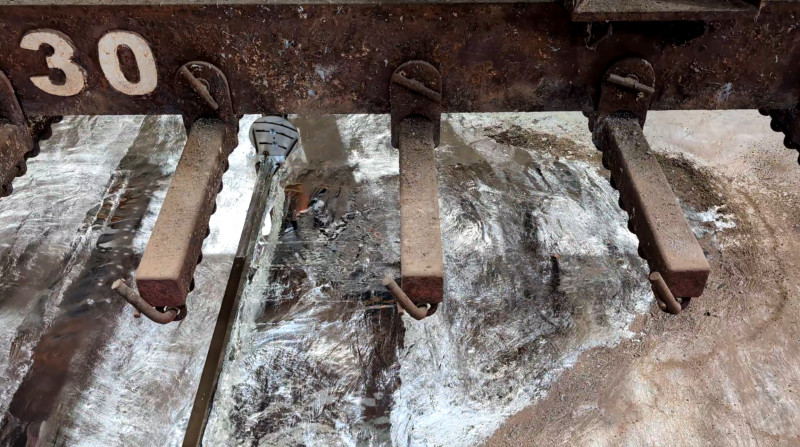
Versuche beim Industriepartner
Basierend auf den Parametern der Vorversuche wurden die definierten Abscheideversuche dann am Industrieverzinkungsofen durchgeführt. Hierzu wurde das gesamte Robotersystem mit Linearachse zu einem Industriepartner (Feuerverzinkerei) transportiert und vor dem Verzinkungskessel installiert.
Um reproduzierbare Versuchsergebnisse zu erzielen, wurde die bei anderen Verzinkungsprozessen entstandene Zinkasche manuell auf die Zinkschmelze aufgebracht. Für die Abscheidevorgänge wurden beide Abscheidewerkzeuge – Düse und Rechen – eingesetzt. Mit dem Rechen als mechanisches Abscheidewerkzeug wurde eine vollständige Entfernung der Zinkasche erreicht.
Felix Oppermann von der RWTH Aachen, erklärt:
„Wir konnten nicht nur die Zinkasche, sondern auch die Zinkoxidschicht erfolgreich entfernen, die sich durch die Oxidation von flüssigem Zink an der Umgebungsluft bildet.“
Gasdurchflussmenge für Effizienz entscheident
Das Bewegungsprofil zum Abstreifen bestand dabei aus einer zunächst langsamen Bewegung des Rechens über die Zinkoberfläche, gefolgt von einer impulsartigen Abstreifbewegung mit Geschwindigkeiten von bis zu 2 m/s, bei welcher Zinkasche sogar in Zonen entfernt werden konnte, die physisch mit dem Rechen nicht erreicht werden können.
Zu einer Kollision mit dem Aufhängungssystem kam es dabei zu keinem Zeitpunkt. Im Gegensatz dazu wurde beim gasbasierten Abscheideprozess die Zinkasche durch Gasbeaufschlagung mobilisiert.
Gunnar Strauß vom Fraunhofer IFF, erläutert:
„Die Gasdurchflussmenge spielt eine entscheidende Rolle für die Effizienz des Prozesses. Wir mussten sicherstellen, dass die Druckluftversorgung optimal war, um die besten Ergebnisse zu erzielen.“
Bei zusätzlichen Versuchen mit Stickstoff als Prozessgas wurde eine erwartungsgemäß geringere Oxidation der Zinkoberfläche im Vergleich zur Verwendung von Druckluft festgestellt. Die technische Machbarkeit der beiden analysierten Abscheidesysteme, sowohl des mechanischen als auch des gasbasierten Systems, wurde im industriellen Maßstab erfolgreich bestätigt.
Ergebnis: Zinkascheabscheidung lässt sich automatisieren
Besonders gute Ergebnisse wurden mit dem mechanischen Abscheidesystem, also dem Einsatz des Rechens, erzielt. Hier war zudem die Geschwindigkeit, mit der die Zinkasche entfernt wurde, deutlich höher. Gute Ergebnisse wurden aber auch mit dem gasbasierten System erzielt, wenngleich hier bei Gasdruck und Gasdurchflussmenge noch Optimierungspotenziale bestehen.
Das Forschungsprojekt hat gezeigt: Der Prozess der Zinkascheabscheidung lässt sich auch im Industriemaßstab mittels Robotertechnik automatisieren. Neben einem deutlichen Effizienzgewinn wurde zudem das wichtige Ziel, die gesundheitlichen Risiken für die Beschäftigten zu senken, in dem Projekt erreicht.
Im weiteren Schritt ist eine engere Kollaboration zwischen Mensch und Roboter vorstellbar. Dies kann noch größere Flexibilitäten in dem Prozess, u.a. beim Herausheben des Verzinkungsgutes, ermöglichen.
Dr. Andreas Voßberg von der BGHM betont:
„Eine Automatisierung des Verzinkungsprozesses kann nicht nur die Sicherheit der Mitarbeiter erhöhen, sondern auch erhebliche Effizienzgewinne im Produktionsprozess ermöglichen.“
(Quelle: Fraunhofer IFF)